Composite Service Solution Project: Composite delamination prediction for a front bumper beam
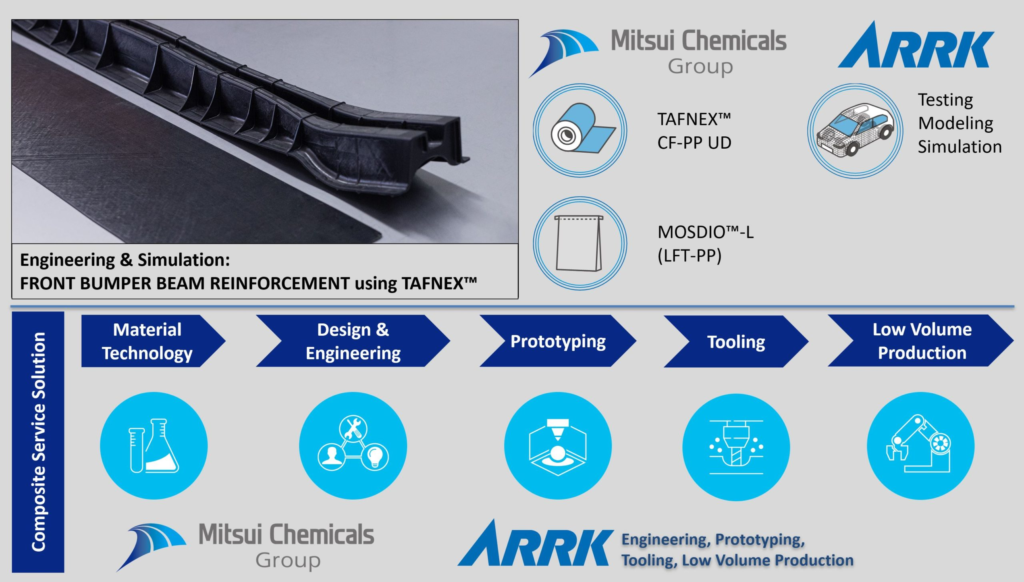
New modelling approach by ARRK Engineering for composite development
Accurate prediction of delamination in composite materials is a challenge and often limits the application of lightweight materials in safety relevant components, as it may reduce the available strength significantly. In order to correctly evaluate delamination of composites while retaining a good runtime performance, a new modeling approach in LS-DYNA® was studied by ARRK Engineering using a full thermoplastic front bumper beam as demonstrator to perform a virtual vehicle evaluation.
Using a new modeling approach from ARRK Engineering, a full-vehicle simulation with TAFNEX™ CF-PP UD from Mitsui Chemicals has shown robust delamination prediction capability while still retaining high run time performance. Thus, the approach can be adopted in full-vehicle crash in order to evaluate composite delamination.
Modeling approach from ARRK Engineering:
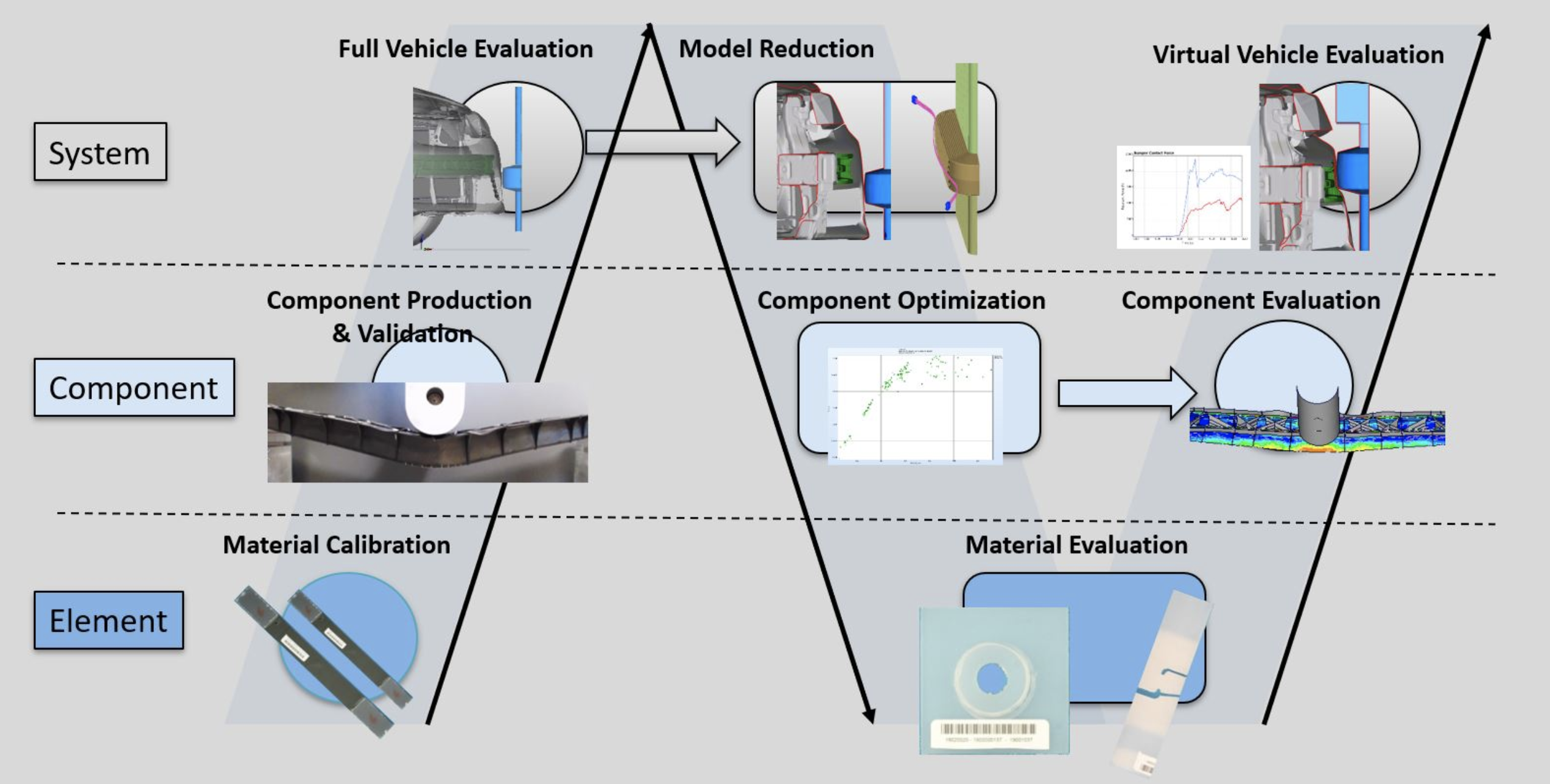
Front Bumper Beam Production
Part Production Value Chain:
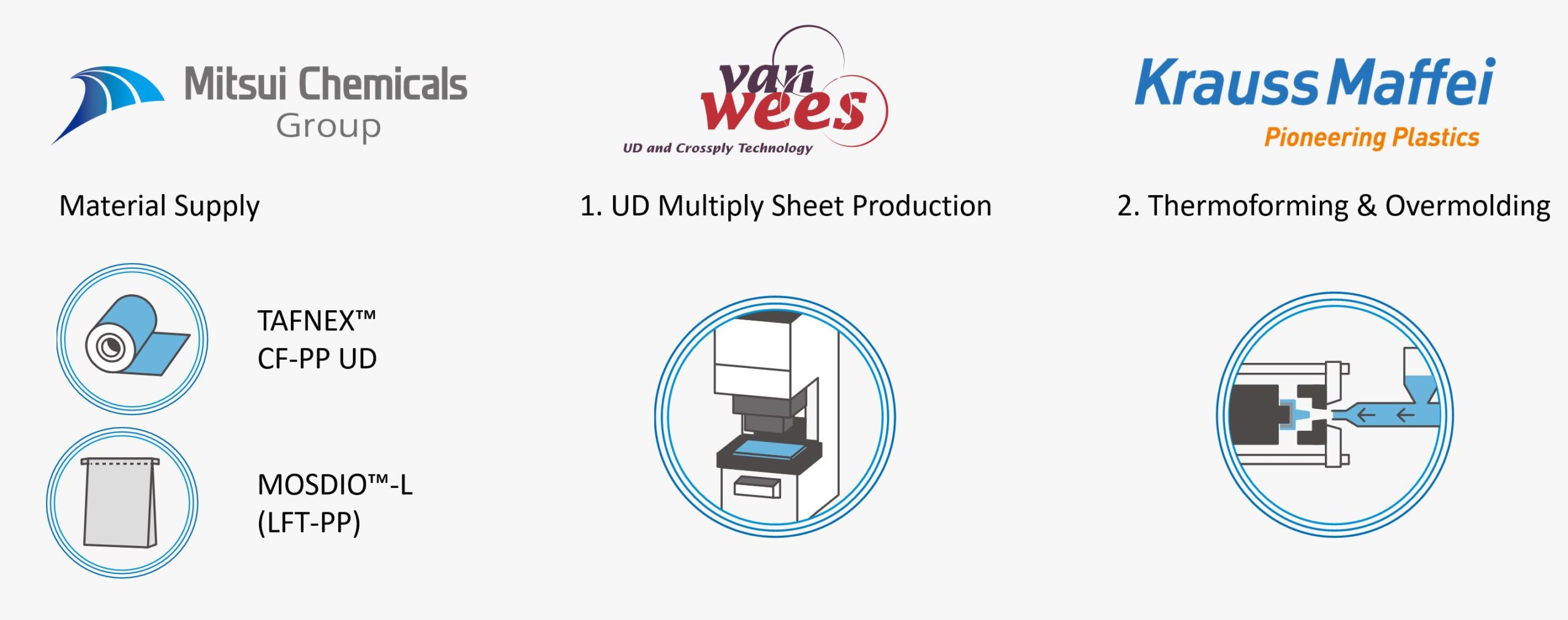
1. Production of UD tape sheets based on multi-axial patches
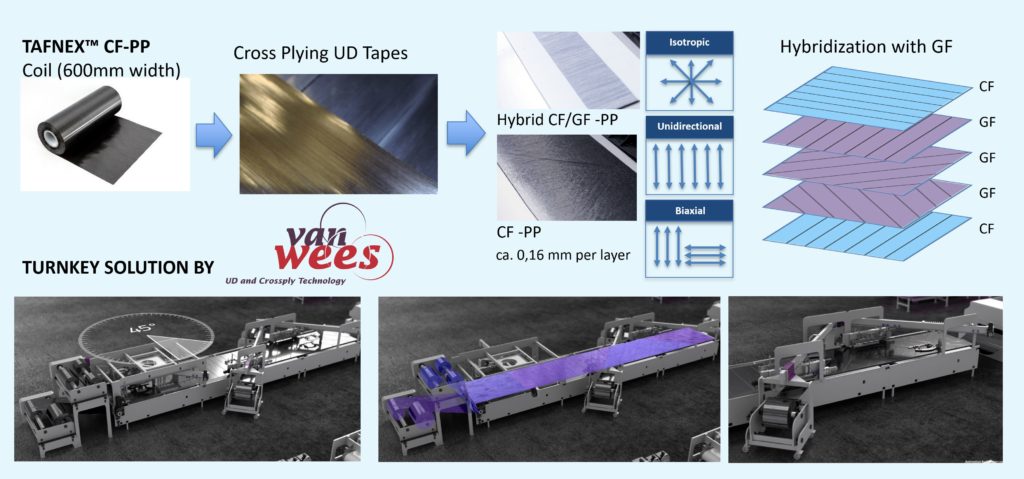
2. Thermoforming and overmolding of UD tape sheet
The FiberForm process developed by KraussMaffei combines the thermoforming of organo sheets and injection molding into one process.
More Information about FiberForm with TAFNEX™
Component and System Evaluation
ARRK Engineering: Validation of material model
- Testing of component and virtual evaluation
- The bumper beam was used for component validation
- Dynamic and quasi-static 3-point bending was investigated
- Results from simulation and test correlate well, showing a high prognostic property of the material car
- Good correlation of load levels and failure mechanism
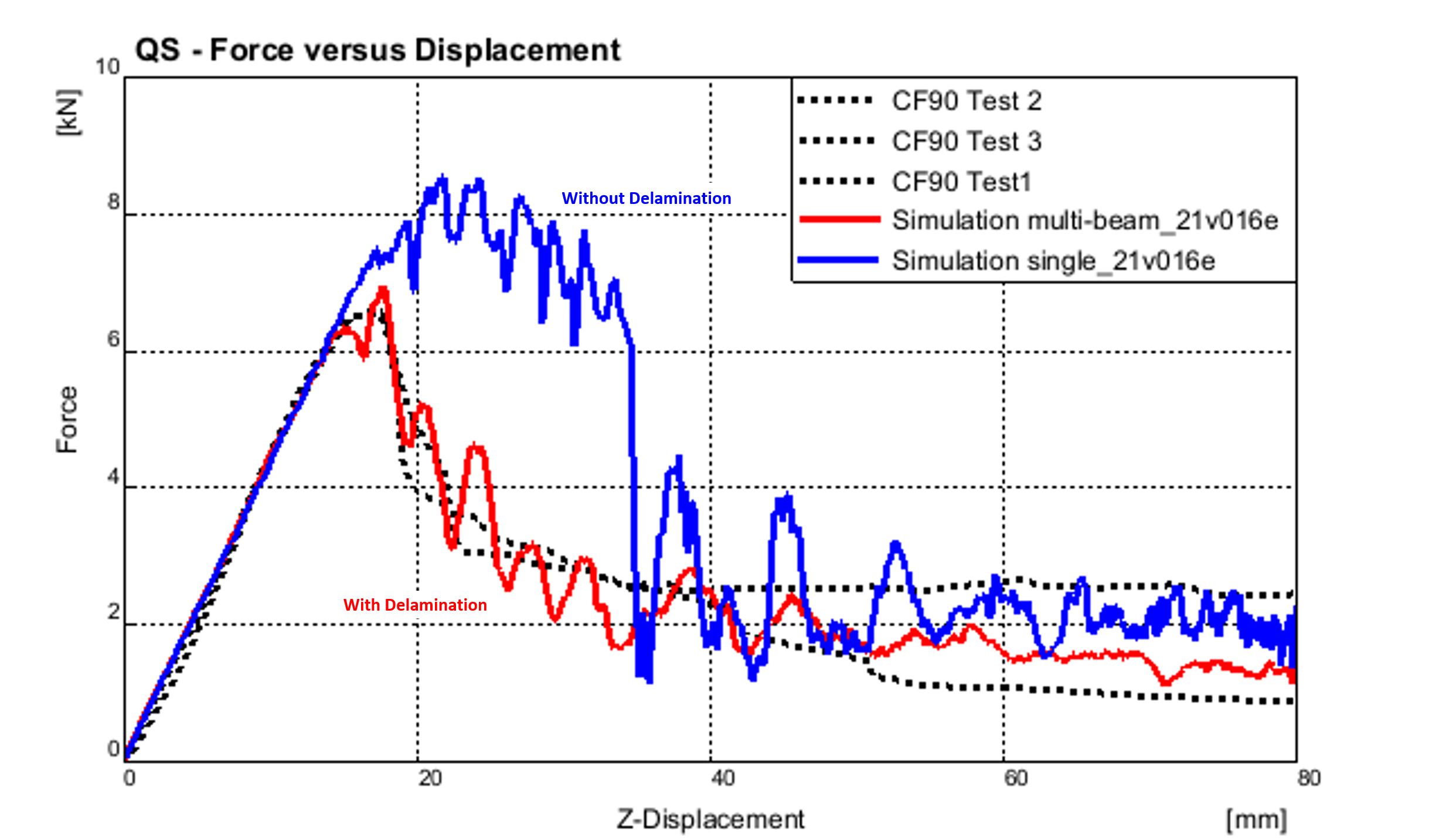
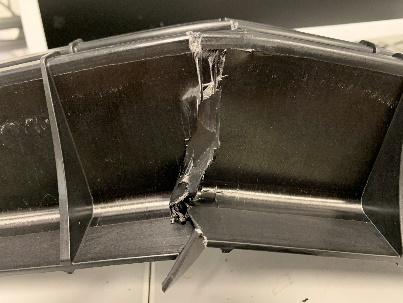
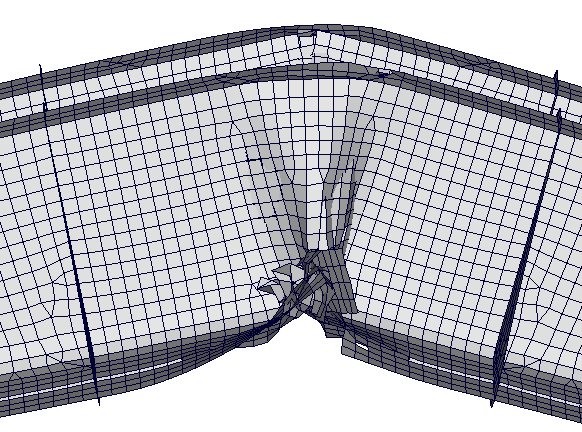
ARRK Engineering: Full vehicle evaluation
The bumper beam was evaluated virtually in a full vehicle setup according to FMVSS-US Part 581 regulation, showing insufficient energy absorption, resulting in significant damage of the cooler. A reduced spring model was created in order to evaluate the energy absorption target derived from full vehicle simulation in a simplified and fast to run simulation model.
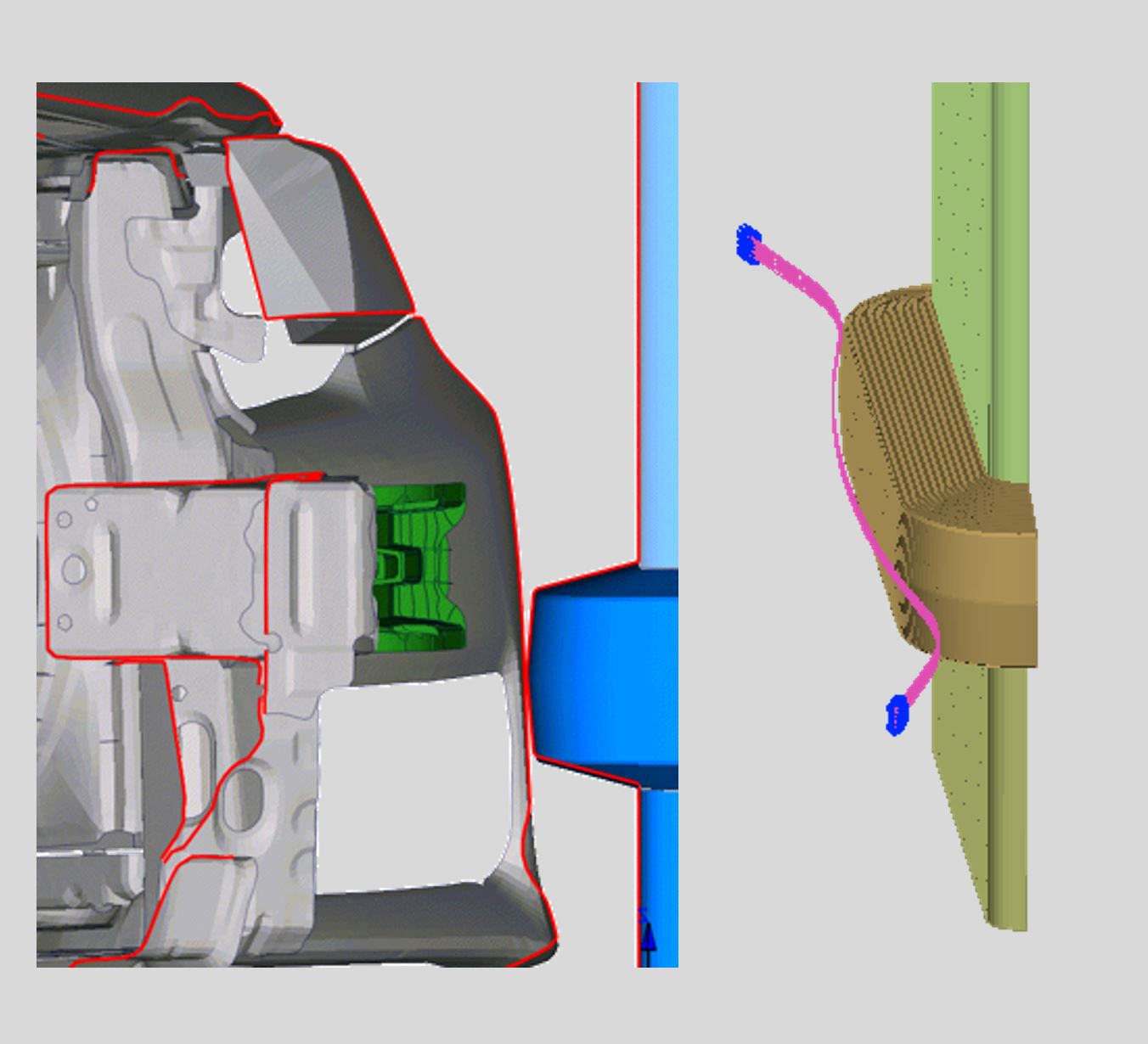
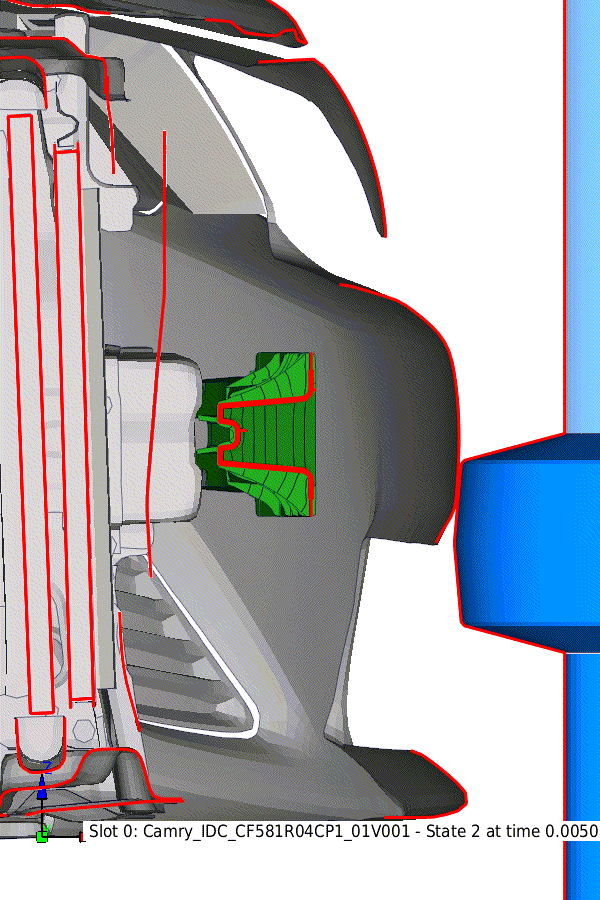
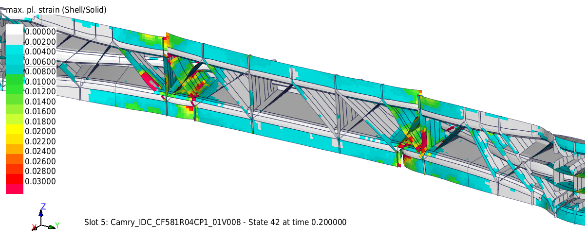
ARRK Engineering: Component optimization
Based on the energy target from full vehicle simulation a parametric study was performed in order to clarify the correlation between stiffness and absorbed energy. The results of this study are used to define a stiffness target and a lay-up to achieve this.
Parametic study to define stiffness target for required energy absorption
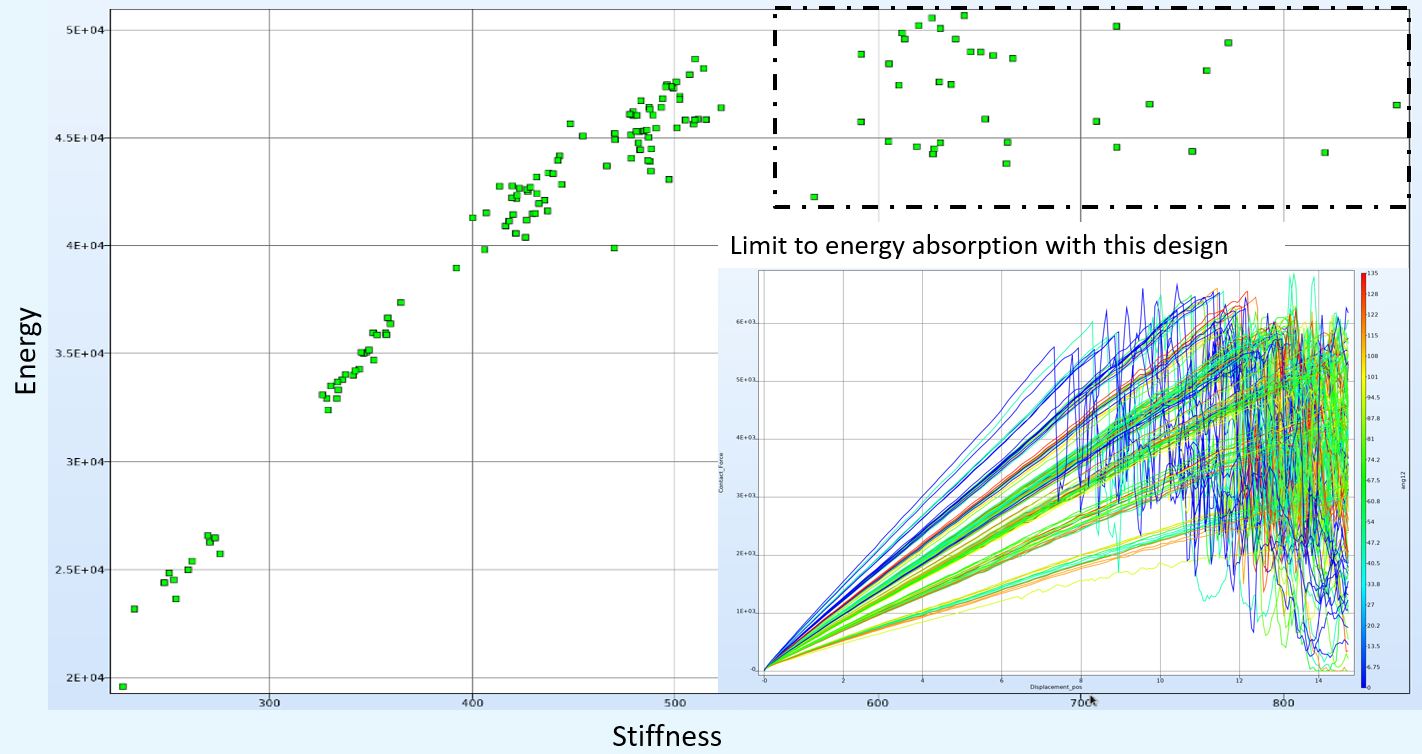
Lay-up change to achieve stiffness target:
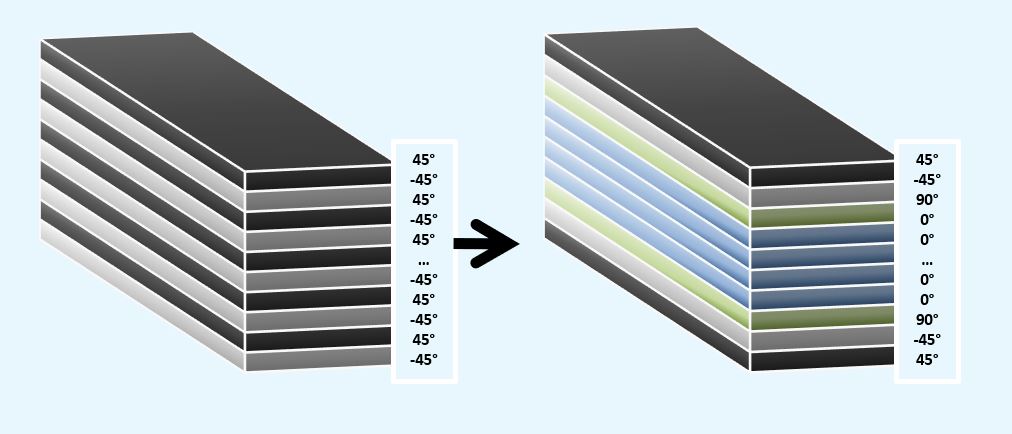
Based on these results a new bumper prototype with optimized lay-up was manufactured
ARRK Engineering: Component reevaluation for improved Lay-up
- A new batch of bumper beams with improved lay-up was produced and tested.
- Load level and stiffness were improved according to prediction.
Deflection of the bumper beam after lay-up change:
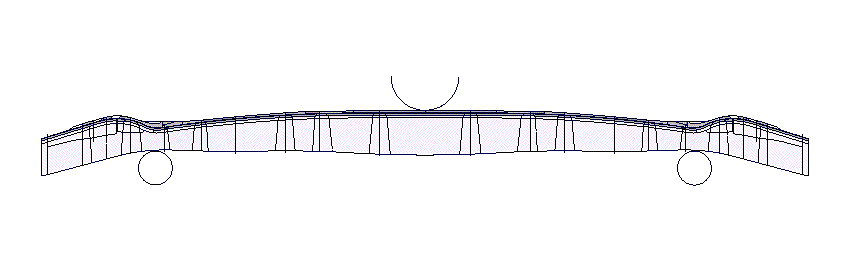
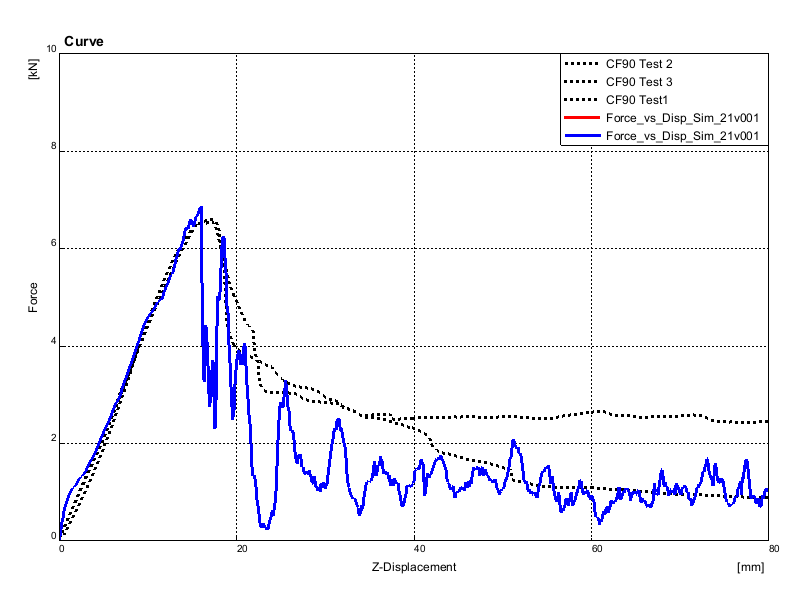
Re-evaluation on Virtual Vehicle and Final Results
ARRK Engineering: Reevaluation on virtual vehicle and final result
The optimised lay-up was re-evaluated in full vehicle model. Contact force and absorbed energy were doubled with less failure occuring and a major decrease in intrusion. Further improvements can easily be achieved by adjusting the design. By using CAE to evaluate material performance early in the development, unnecessary but costly tooling, prototyping and testing can be reduced.
Virtual vehicle results after lay-up change:
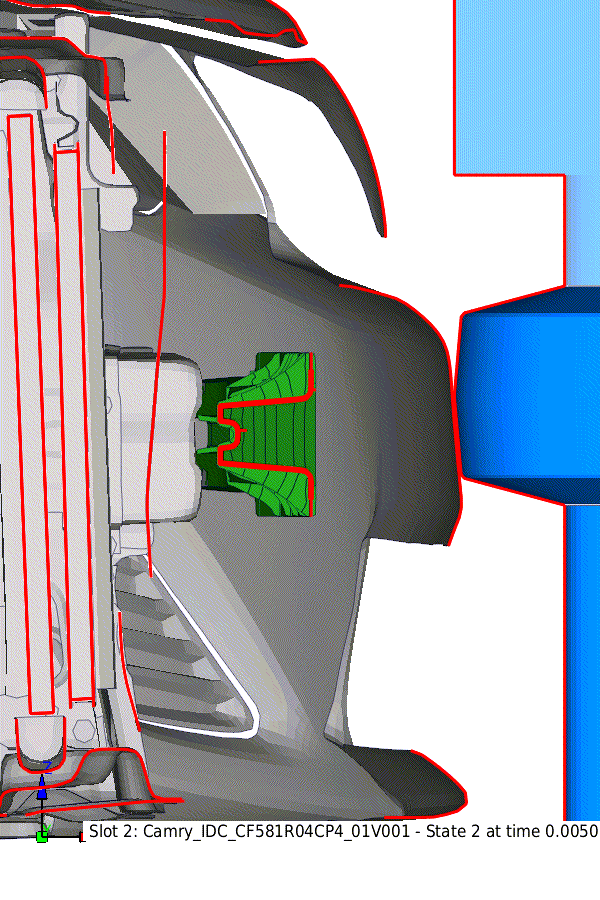
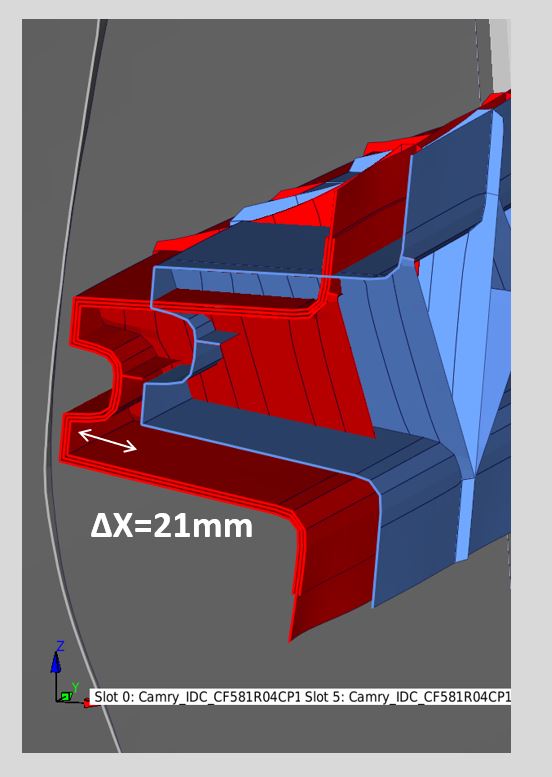
Final result: Comparison of original lay-up and newlay-up:
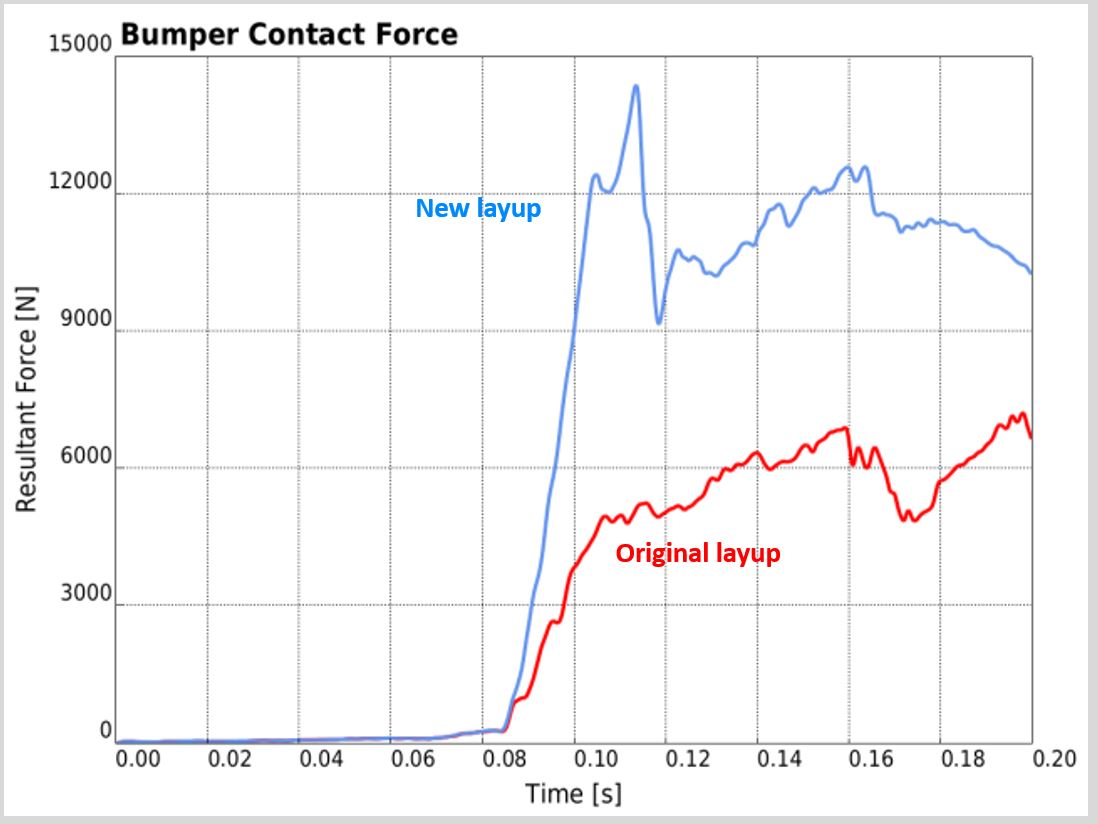
The new stacked shell modeling approach from ARRK Engineering has shown promising results at coupon and component level. At the full-vehicle simulation scale, the new modeling approach has presented robust delamination prediction capability while still retaining high run time performance. Thus, the approach can be adopted in full-vehicle crash in order to evaluate composite delamination.
Mitsui Chemicals and ARRK Engineering are looking forward to new opportunities and component evaluation using TAFNEX™ CF-PP UD.
Related Cases
Local reinforcement of a tailgate
Mechanical properties increased by adding TAFNEX™ CF-PP UD in the injection molding process
Automotive Interior Demonstrator
Process Development for an interior automotive part in cooperation with HRC Group
Functionalization of thermoplastic profiles
Together with our partners ANYBRID GmbH, INOMETA GmbH and the Institute for Lightweight Construction and Plastics Technology at the Technical University of Dresden, we have rethought the functionalization of high-performance…